Secondary container labeling plays a critical role in workplace safety and regulatory compliance, ensuring that hazardous chemicals are clearly identified and handled correctly. These labels provide vital hazard information, making it easier for employees and visitors to recognize potential risks and take appropriate precautions.
Health and safety officers, Environmental Health and Safety (EHS) departments, lab managers, and facilities managers shoulder the responsibility of maintaining Occupational Safety and Health Administration (OSHA) compliance. Accurate and compliant labeling isn’t just about meeting legal requirements—it’s about creating a safer work environment for everyone.
With M3V’s SDS solution, these professionals gain a powerful tool to streamline SDS management and secondary container labeling processes. By providing a customizable, user-friendly system for creating compliant labels, M3V Software helps equip organizations to comply.
Why Proper Labeling of Secondary
Containers Matters for Health & Safety
According to OSHA, American workers suffer over 190,000 illnesses and 50,000 deaths related to chemical exposures a year.
Proper labeling of secondary containers is not just a regulatory requirement—it’s a cornerstone of workplace safety. Secondary container labels ensure that vital hazard information is readily available, reducing the risk of accidents and protecting employees from exposure to hazardous chemicals. Clear and accurate labeling also empowers workers to make informed decisions when handling, transporting, or storing chemicals.
Benefits of Secondary Container Labeling for Key Roles
- Health and Safety Officers: Clear secondary container labels support safe practices across the workplace by providing quick access to critical hazard information. Labels with clear hazard warnings and precautionary statements help prevent accidents and ensure compliance with OSHA’s Hazard Communication Standard.
- Lab Managers and Chemical Supervisors: In laboratory and industrial settings, accurate secondary container labeling ensures that chemical names, hazard classifications, and signal words are easily accessible during chemical handling. This is particularly important when dealing with smaller containers like spray bottles that are frequently used in day-to-day operations.
- HR & EHS Departments: For HR and Environmental Health and Safety teams, secondary container labels simplify compliance and reporting. Whether preparing for audits or managing the workplace label requirements outlined in OSHA guidelines, properly labeled containers streamline documentation and improve overall safety communication.
Understanding OSHA Requirements
for Secondary Container Labels
Compliance with OSHA’s Globally Harmonized System (GHS) standards is critical for secondary container labels to maintain workplace safety and avoid regulatory penalties. These standards ensure that every employee has access to consistent and clear hazard communication, regardless of whether they are handling a primary container or a secondary container.
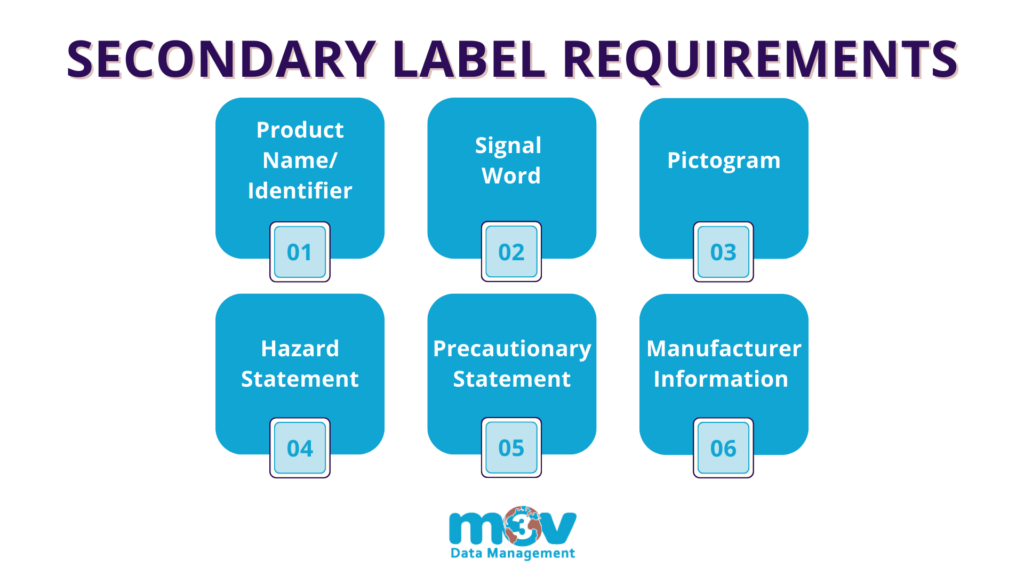
Key OSHA GHS Standards for Secondary Containers
To ensure workplace safety and regulatory compliance, OSHA mandates specific labeling requirements for hazardous or potentially hazardous chemicals in secondary containers. While these labels are simpler than those for primary containers, they must still include essential elements outlined under the OSHA Hazard Communication Standard:
Required Elements for Secondary Container Labels:
- Product Name/Identifier: The chemical name or identifier must match what is listed in the Safety Data Sheet (SDS). This helps employees quickly recognize the material and its associated hazards.
- Signal Word: Indicating the level of hazard (e.g., “Danger” for severe hazards or “Warning” for less severe hazards).
- Pictogram: Standardized hazard symbols that visually communicate specific risks.
- Hazard Statement: A description of the nature and degree of the chemical’s risks (e.g., “Flammable liquid and vapor”).
- Precautionary Statement: Guidance on handling, storage, and emergency measures to minimize risk.
- Name, Address, and Telephone Number of Manufacturer or Responsible Party: This provides traceability and a point of contact for further information or in case of emergencies.
Although these requirements are less strict than those for primary containers, they must be supported by accessible safety data, such as SDS documents, to provide detailed hazard and precautionary information.
Flexible Guidelines for Specific Situations
OSHA recognizes the need for flexibility in certain scenarios, such as small containers or portable containers used by a single employee during a single work shift. In such cases, simplified labeling methods or alternative approaches may be permissible. However, these exceptions must still prioritize safety and ensure that hazard information is available when needed.
How M3V’s SDS Labeling Solution Supports
Compliance and Simplifies Labeling Processes
M3V’s SDS software is designed to make SDS management and secondary container labeling fast, accurate, and fully compliant with OSHA and GHS standards. With features tailored for workplace safety and operational efficiency, it’s a comprehensive software solution for health and safety professionals.
Streamlined GHS-Compliant Labels
Creating secondary container labels is simple and efficient with M3V. The platform enables users to quickly generate labels that include all required GHS elements, such as signal words, hazard pictograms, and precautionary statements.
Enhanced Accessibility with QR Codes
Labels can include QR codes that link directly to the associated SDS, providing instant access to critical hazard information on any smartphone. This feature ensures that employees and first responders can quickly view safety data during emergencies or routine handling of hazardous materials.
Customizable Label Sizes and Formats
The platform offers flexibility to design labels for various container sizes and shapes, making it ideal for labs, facilities, and chemical storage areas. Whether it’s a small spray bottle or a large waste container, labels can be tailored to fit specific needs.
Data Management and Control for EHS and Operations
M3V’s solution gives full ownership of SDS data, with options to export, save, and access information offline. This ensures seamless compliance management across departments while maintaining data control.
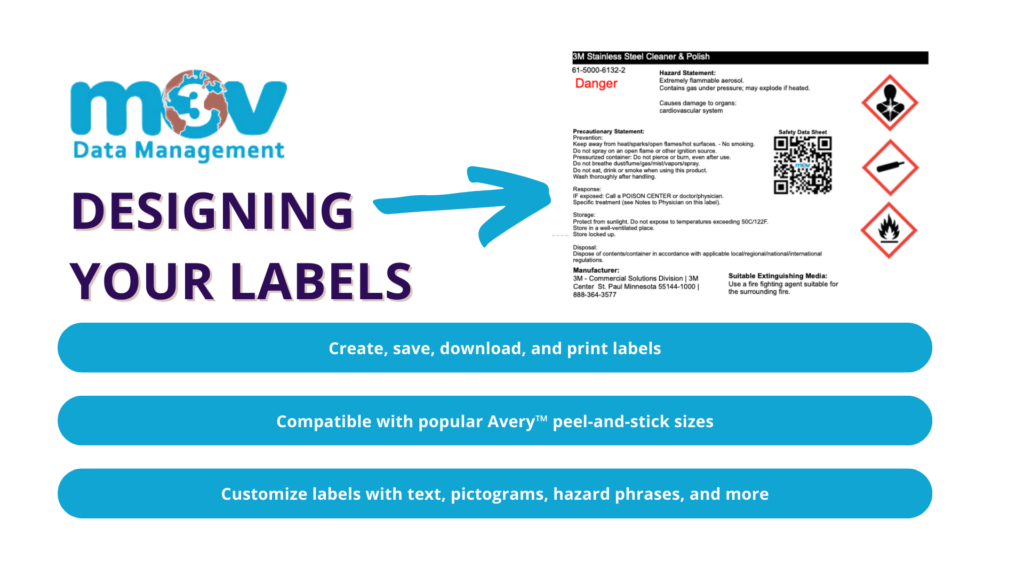
Design Your Own Labels with Ease
- Create, save, download, and print labels.
- Compatible with popular Avery™ peel-and-stick sizes, including:
- 2 ⅝” x 1”
- 2” x 4”
- 4” x 3 ⅓”
- 5” x 7”
- 8” 1/2 x 11”
- Customize labels with text, pictograms, hazard phrases, and more.
Available for free with our SDS Explorer Software!
Key Benefits of M3V for Health & Safety Professionals
M3V delivers essential advantages for health and safety officers, lab managers, and EHS teams who need efficient, cost-effective tools for compliance and workplace safety.
- Safety and Compliance Assurance: M3V’s solution enhances workplace safety by ensuring that you have the tools you need to design OSHA/GHS-compliant labels, reducing the risk of accidents and regulatory penalties.
- Time-Efficient Labeling: In high-stakes situations, such as lab procedures or medical emergencies, M3V’s system allows for quick and accurate labeling to ensure employees have the information they need when they need it.
- Cost-Effective SDS Management Solution: M3V Software provides a customizable and affordable labeling solution that reduces overhead while meeting compliance goals.
Enhance Workplace Safety and Compliance with M3V Software
Ready to take your hazard communication program to the next level? Request a demo or consultation today to see how M3V Software’s SDS Labeling Solution can meet your unique needs and support your safety and compliance goals.