For professionals managing hazardous chemicals or ensuring workplace safety, understanding SDS update requirements is critical. However, the specific obligations vary depending on your role. Are you a chemical manufacturer, responsible for authoring the SDS? Or are you an employer tasked with maintaining compliance for your work area under OSHA or WHMIS standards?
This blog breaks down the regulatory requirements for both groups, explaining when SDS updates are necessary and why keeping your SDS information accurate is essential. Whether you’re navigating the Hazard Communication Standard in the United States or dealing with WHMIS legislation in Canada, this guide will help you manage your SDSs effectively while protecting your workplace and meeting regulatory requirements.
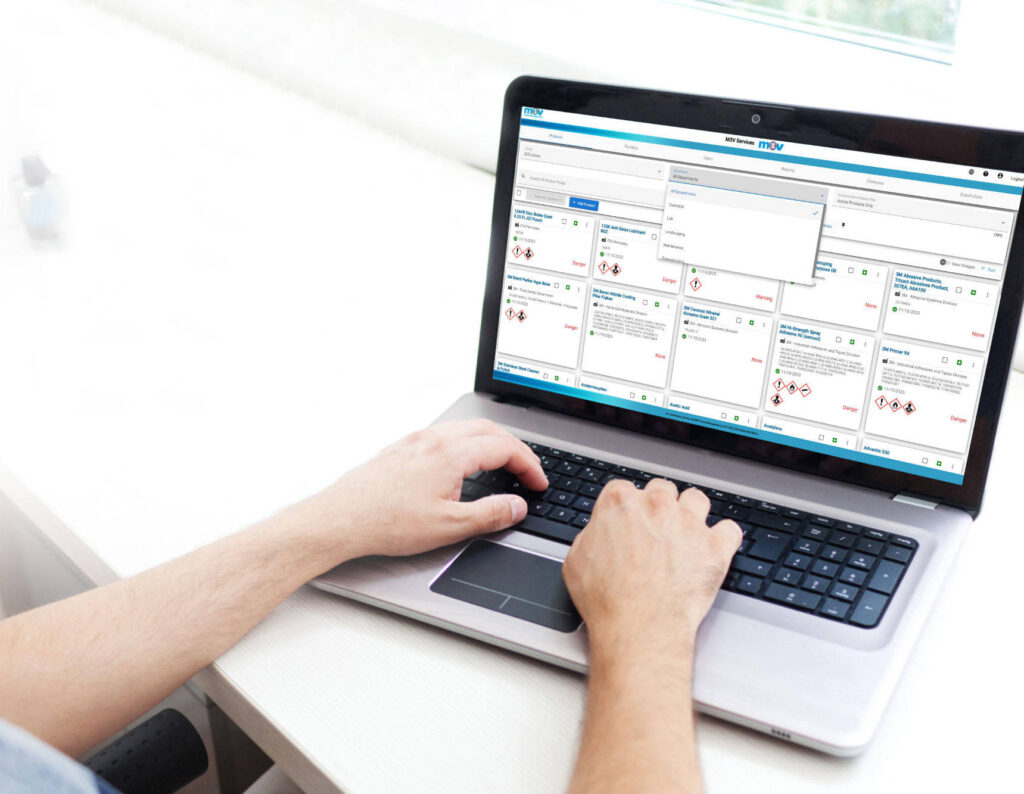
What Is an SDS and Why Is It Important?
A Safety Data Sheet (SDS) is a cornerstone of chemical safety and hazard communication. Designed to convey critical information about hazardous substances, SDSs provide detailed descriptions of chemical properties, hazard classifications, and protective measures. Reducing the risk of accidents and protecting employees from exposure to hazardous chemicals, an SDS ensures that downstream users and employees have access to the information they need to stay safe.
The responsibilities surrounding SDSs differ significantly between manufacturers and employers:
- Chemical Manufacturers and Suppliers: These entities are required to create and maintain SDSs for every chemical product they produce or distribute. The Hazardous Products Act and OSHA regulations require that SDSs include significant information about chemical hazards, exposure scenarios, and safety precautions.
- Employers: While employers do not author SDSs, they are responsible for ensuring that the safety information provided by manufacturers is readily available in their workplace. This often includes maintaining an organized SDS library, training employees on occupational safety, and ensuring compliance with relevant standards like the OSHA Hazard Communication Standard.
By maintaining accurate and up-to-date SDSs, both manufacturers and employers contribute to safer, more informed work environments. Updated SDSs help prevent workplace incidents, ensure compliance during inspections, and support a culture of safety through easy electronic access to critical information.
For Manufacturers: When Is an SDS Required to Be Updated?
For chemical manufacturers and suppliers, creating and maintaining Safety Data Sheets (SDSs) is a critical responsibility. The OSHA Hazard Communication Standard (HCS) provides detailed guidelines for when an SDS must be reviewed and revised. Specifically, manufacturers are required to update the SDS within three months of identifying new significant information about the hazards of a chemical or following changes in regulatory requirements.
Examples of triggers for updating an SDS include:
- New Hazard Information: If new data about a hazardous chemical is discovered—such as changes to its hazard classification or newly identified risks—manufacturers must incorporate this information into the SDS.
- Regulatory Revisions: Updates to the OSHA HCS, including those aligned with GHS criteria, may require SDS modifications. In cases where hazard classifications remain unchanged but the SDS format has been updated, manufacturers should verify state-specific requirements under EPCRA for submitting modified SDSs.
Additionally, when new hazard information is identified, labels associated with the chemical must also be revised within six months, ensuring that any chemical shipped after this period reflects the updated safety details. For chemicals that are not currently being imported or produced, these updates must be completed before the product re-enters the workplace.
For Employers: Who Bears the Responsibility?
Unlike manufacturers, employers are not responsible for authoring or modifying the content of Safety Data Sheets (SDSs). However, they do play a crucial role in ensuring that SDS information is readily available and up-to-date in the workplace. Employers must maintain compliance with OSHA regulations and WHMIS legislation by keeping the most recent SDS versions provided by manufacturers or chemical suppliers accessible to employees and other stakeholders.
Recommended Practices for Employers:
- Regularly Check for Updates: Proactively reach out to your chemical supplier or manufacturer to confirm whether any updates to an SDS have been issued, particularly following the initial shipment of a new chemical product.
- Conduct Periodic Audits: Perform annual or semi-annual reviews of your SDS library to ensure all information is current and meets the standards of your work area. A comprehensive wall-to-wall chemical inventory is a vital component of these audits. With M3V Data Management, you can easily print out a chemical inventory list by area or department, providing a clear starting point for your inventory project. This helps identify any missing or outdated SDSs, ensuring compliance and workplace safety.
- Use SDS Management Tools: Simplify tracking and organizing SDS updates by providing employees with easy, direct access to your SDS software database. Tools such as a direct login link or printable large peel-and-stick QR codes can significantly reduce barriers to employee access, a key principle emphasized in the OSHA Hazard Communication Standard. These features ensure that employees can quickly and effortlessly access critical safety information, supporting compliance and fostering a safer work environment.
Avoiding Compliance Pitfalls
Outdated SDS information can have serious consequences for both manufacturers and employers, ranging from regulatory penalties to increased safety risks. Here are the potential pitfalls of neglecting SDS updates:
Non-Compliance with Regulations
Failing to maintain accurate SDSs violates the OSHA Hazard Communication Standard and other regulatory frameworks. Non-compliance can lead to significant fines, legal penalties, and negative audit outcomes.
Workplace Safety Risks
Incomplete or outdated SDSs compromise the ability to communicate critical information about hazardous substances, such as recommended protective measures or handling instructions. This can result in workplace accidents, chemical exposures, or misuse of protective equipment.
Reputational Damage
A company’s reputation can suffer if chemical hazards are mishandled or if incidents occur due to outdated or incomplete safety information. Trust from employees, regulators, and clients may be eroded, impacting business relationships.
M3V Data Management
For employers, investing in a reliable SDS management system helps mitigate these risks. Features like electronic access and robust organizational tools ensure your SDS information is always accurate and accessible. M3V’s solutions are trusted by a diverse range of clients, including manufacturers, healthcare organizations (hospitals, medical and dental offices), zoos, federal correctional facilities, the Federal Bureau of Land Management, airports, municipal governments such as the City of Milwaukee and the City of Las Vegas, as well as school districts and universities.
How M3V Data Management Can Help Employers with SDS Compliance
Managing Safety Data Sheets (SDSs) is no small task, but M3V Data Management provides the tools and expertise to make the process seamless. Our web-based software applications, like SDS Explorer and Chemical Management Navigator (CMN), are specifically designed to meet the needs of EH&S managers, ensuring compliance with OSHA regulations, WHMIS legislation, and other standards.
Key Features of M3V’s SDS Management Solutions:
- Automated Database Updates: For customers subscribed to our global library, we automatically update their database with the latest SDSs as we receive them from manufacturers. Employers can easily run automated reports at any time to view recent activity, such as new additions or updates to their database. While we ensure seamless updates to the database, employers are encouraged to periodically review reports to stay informed of changes and maintain compliance.
- Periodic Review Tools: M3V software simplifies SDS revisions with built-in features for conducting regular audits. These tools allow you to verify compliance and address potential gaps in your occupational safety program with ease.
- Customizable Platforms: Tailor your SDS management system to fit your specific needs. Whether you’re organizing chemical hazards by department or cross-referencing chemical properties for regulatory reporting, our software adapts to your organization’s requirements.
With a proven track record of supporting EH&S managers since 2002, M3V Data Management offers affordable, intuitive solutions backed by exceptional customer service. Our software helps you reduce the administrative burden of SDS compliance, ensuring you focus on what matters most—keeping your team safe and your business running smoothly.
Conclusion: Updating & Maintaining SDS Sheets
The question of how often an SDS needs to be updated depends on whether you are a manufacturer or an employer. Manufacturers are required to revise SDSs whenever significant new data becomes available or when regulations change, while employers must ensure that they have the most up-to-date SDS information in their work area.
Maintaining accurate SDSs is more than a regulatory obligation—it’s a critical component of workplace safety. By keeping employees informed about chemical hazards and ensuring compliance with standards like the OSHA Hazard Communication Standard, businesses can minimize risks and avoid costly penalties.
Ready to simplify your SDS management? M3V Data Management offers innovative, user-friendly solutions to streamline compliance and protect your workforce. Contact us today to schedule a demo and see how our software can transform your approach to SDS requirements.
Sources: