The Globally Harmonized System of Classification (GHS) is an internationally recognized system designed to standardize and harmonize the classification and labeling of chemical substances. GHS compliance ensures that businesses manage hazardous chemicals in a consistent and universally understood manner, improving safety and reducing the risk of accidents or mishandling. This system provides a unified approach to identifying chemical hazards, labeling substances, and offering appropriate safety instructions to workers.
For industries like manufacturing, education, municipalities, and much more, GHS compliance is essential not just for workplace safety but for meeting regulatory compliance. It helps organizations mitigate risks, promote safe chemical handling, and protect workers from potentially harmful substances. Failing to comply with GHS regulations can result in penalties, legal issues, and increased safety hazards.
GHS compliance is vital in connecting workplace safety with regulatory standards. Global standards like the European Union’s REACH regulation and U.S. regulations under OSHA ensure that businesses properly classify chemicals and communicate hazards clearly. In Canada, WHMIS (Workplace Hazardous Materials Information System) aligns with GHS requirements to ensure that workers are informed and protected. By meeting these international, U.S., and Canadian hazardous products regulations, businesses foster safer environments and remain compliant with local and global standards.
Key Components of GHS Compliance
The foundation of GHS compliance lies in clear and consistent hazard communication. Key to this communication is Safety Data Sheets (SDS), which provide detailed information about chemicals, their hazards, and how to safely handle, store, and dispose of them. A compliant safety data sheet includes 16 standardized sections, ranging from chemical properties to first aid measures, and plays a critical role in ensuring that employees and responders have the information they need to handle chemicals safely. By maintaining accurate and up-to-date SDS, businesses comply with GHS regulations and promote a safer work environment.
Another essential element of GHS compliance is chemical classification. GHS guidelines categorize chemicals based on their hazards, considering factors like toxicity, flammability, and environmental impact. Proper classification ensures that chemicals are accurately identified, and their risks are clearly communicated to workers through labels and safety instructions.
The hazard communication standards set by GHS are pivotal in labeling hazardous chemicals. These standards specify the use of standardized labels, which are designed to communicate hazards clearly and effectively. This system helps employees easily identify the risks associated with chemicals and take the necessary precautions.
GHS labels are designed with simplicity and clarity in mind, focusing on key information that workers need to stay safe. The labels feature signal words, hazard statements, and precautionary statements.
Lastly, chemicals are classified into three broad categories based on the type of hazard they present: physical, health, and environmental hazards.
- Physical Hazards include risks such as flammability, corrosivity, and explosiveness.
- Health Hazards addresses the impact chemicals can have on human health, such as causing cancer, respiratory issues, or skin damage.
- Environmental Hazards highlight the potential for chemicals to harm the environment, including aquatic toxicity and ozone depletion.
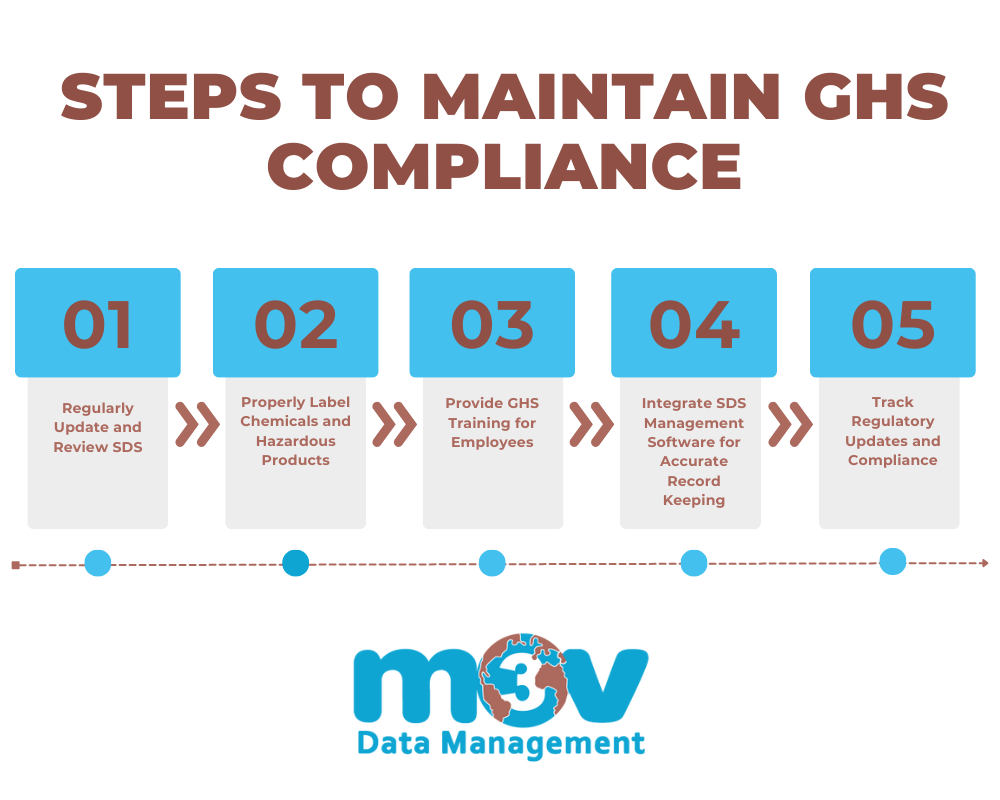
Steps for Businesses to Maintain GHS Compliance
Maintaining GHS compliance requires ongoing attention to detail, regular updates, and a commitment to safety. Here’s how businesses can ensure they stay compliant:
1. Regularly Update and Review SDS for All Chemicals
One of the most important steps in GHS compliance is ensuring that Safety Data Sheets (SDS) are always up to date. Chemical manufacturers ideally update their SDS every 3-5 years, but businesses should check for updates more frequently, especially when new regulations come into play. Using SDS management software allows businesses to automatically receive updated documents directly from manufacturers, ensuring they never miss important updates.
2.Proper Labeling of Chemicals and Hazardous Products
Proper labeling is a cornerstone of GHS compliance. All chemicals and hazardous products must be labeled per GHS standards. Labels should include:
- GHS Symbols to visually communicate hazards.
- Signal Words like “Danger” or “Warning” to indicate the severity of the risk.
- Hazard Statements that describe the type of hazard (e.g., “Toxic if inhaled”).
- Precautionary Statements that provide recommendations for safe handling, storage, and disposal.
Labels should be durable, legible, and affixed in visible locations on chemical containers. To simplify the process, labeling software can automatically generate compliant labels based on the chemical’s classification, reducing manual errors and improving efficiency.
3. Provide GHS Training for Employees
Employee education is essential for GHS compliance. Staff should be trained to:
- Read and understand GHS labels and SDS.
- Recognize hazard symbols and what they signify.
- Follow proper handling procedures for chemicals based on their classification.
Employees should also be familiar with the 16 sections of an SDS and what each one communicates about chemical properties, handling precautions, and emergency responses. Regular training sessions help keep employees updated on new regulations, products, and procedures.
4. Integrate SDS Management Software for Accurate Record Keeping
An efficient SDS management system helps businesses automate the process of receiving, updating, and storing SDS. The software can track compliance, monitor regulatory updates, and maintain an organized SDS library. In addition, businesses can provide instant access to SDS during emergencies, enhancing workplace safety and ensuring a swift response when needed.
5. Track Regulatory Updates and Compliance
GHS compliance doesn’t stop at updating SDS and labeling. Businesses must track ongoing changes to regulations from bodies like OSHA, REACH, and WHMIS. Regularly running reports to compare your chemical inventory against updated regulatory lists helps ensure that your business is always aligned with evolving laws.
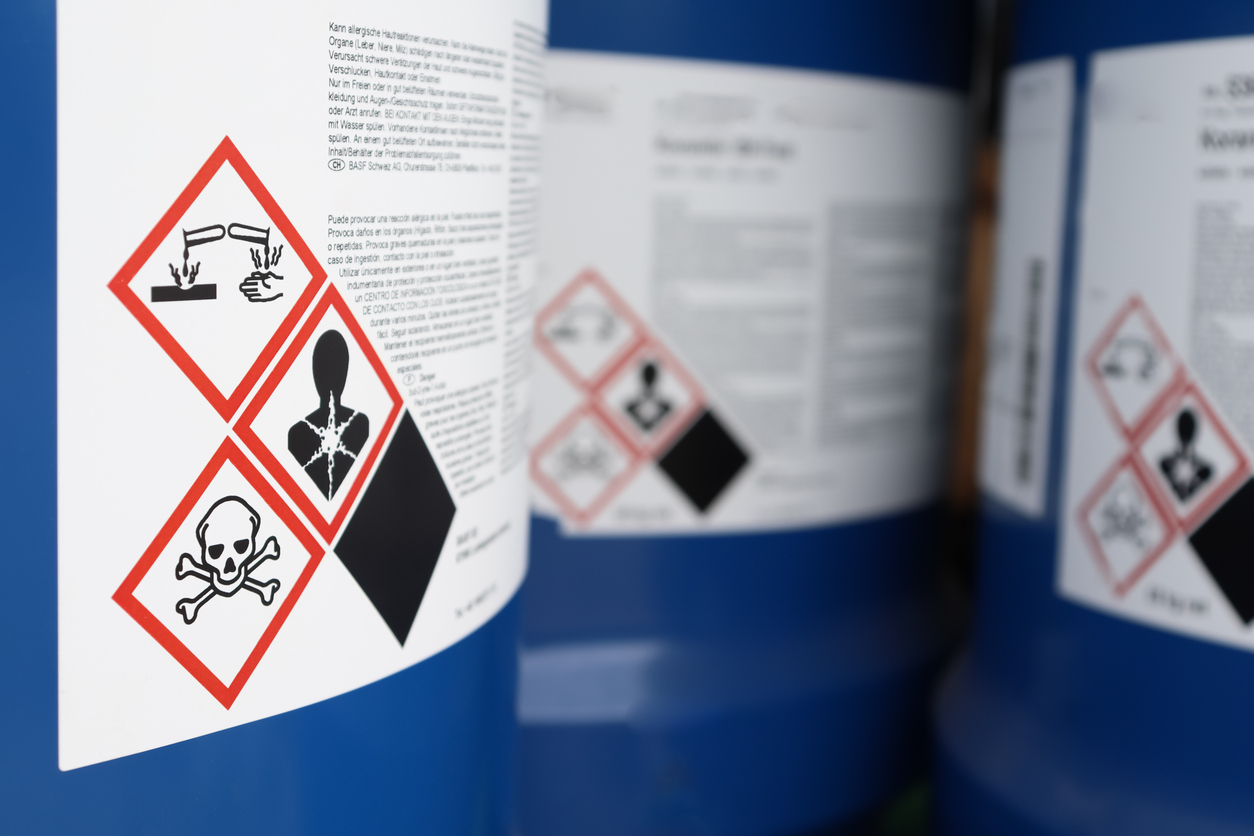
Common Challenges with GHS Compliance
Managing GHS compliance can be complex, especially for businesses handling large volumes of hazardous chemicals. Some common challenges that arise include:
1. Managing Large Volumes of Hazardous Chemicals
Tracking multiple SDSs and ensuring proper labeling for each chemical can be overwhelming and time-consuming, especially as the number of chemicals grows.
2. Keeping Up with Regulatory Updates
GHS guidelines and regulations change frequently. Staying updated with the latest changes from agencies like OSHA, REACH, and WHMIS can be a challenge, and missing these updates can result in non-compliance.
3. Employee Training
Ensuring that employees are consistently trained on GHS labeling, SDS interpretation, and chemical handling is crucial. Ongoing training is necessary to keep up with new chemical information and regulations.
Solutions: Implementing SDS Management Software
The solution lies in using SDS management software to:
- Automate updates and ensure the latest SDS are always on hand.
- Streamline training and track employee progress.
- Organize chemical inventories efficiently, making compliance easier to maintain.
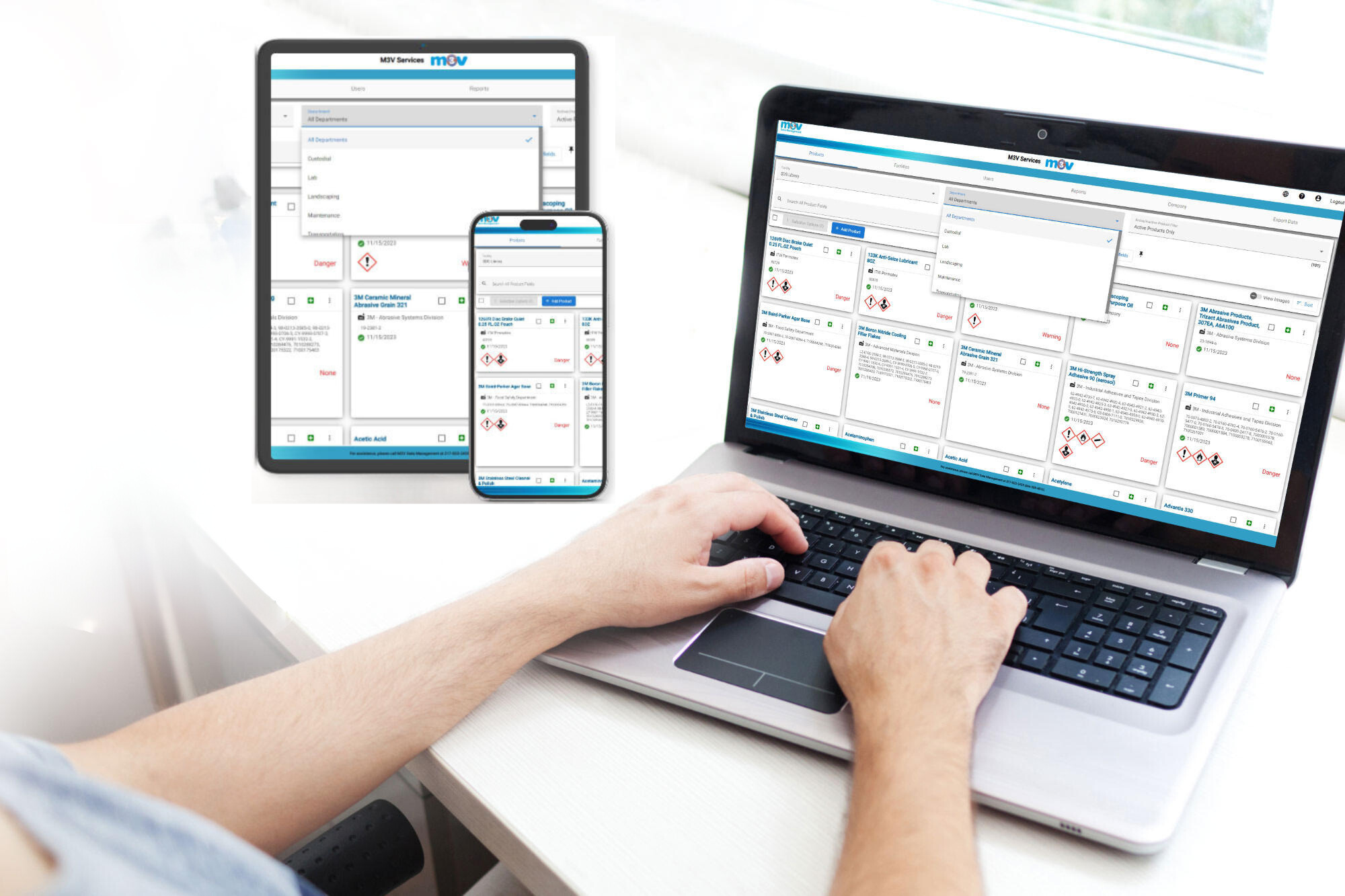
Stay GHS Compliant with M3V
If you’re looking for a straightforward and effective solution to meet GHS compliance requirements, M3V Data Management is here to help. Our platform simplifies Safety Data Sheet (SDS) management, helping you stay up-to-date with regulatory requirements and ensuring safety data is always accessible and accurate.
Simplify Hazard Communication and Ensure Compliance
M3V Data Management streamlines hazard communication by providing clear and consistent access to SDS, ensuring that your team is well-informed about chemical hazards and handling procedures. With our system, you can easily track and update chemical classifications, labels, and safety protocols.
As regulations evolve, M3V helps you stay ahead by offering a flexible platform that adapts to new compliance requirements. With M3V, you can confidently manage your chemical safety data, reduce risk, and maintain compliance.
Ready to simplify your GHS compliance? Get in touch with M3V Data Management today to learn how our solutions can streamline your SDS management and improve workplace safety.